Keeping equipment working at optimal performance with less downtime and supporting a longer life span are significant factors that make fire-resistant hydraulic fluids a safe and pragmatic choice. As in any hydraulic system, a strong maintenance strategy is vital to reduce component corrosion and thereby avoid the significant costs of replacing parts and unplanned repair downtime. Therefore, a disciplined maintenance regime for water-glycol (HFC) hydraulic fluids can help keep systems operating more effectively and efficiently — and for longer.
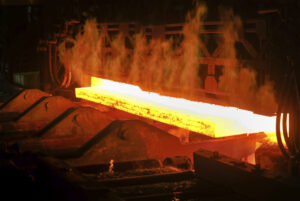
Reliable performance with less downtime
Standing at 50 to 55% market adoption, HFC is a water-based fluid that can be used in all industries where there are major fire risks. HFC hydraulic fluids remain the most widely used fire-resistant hydraulic fluids today because of their price ratio and combination of excellent fire-resistant properties with good lubrication performance.
Hydraulic fluids with HFC technology have low flammability. They can be used in the presence of a high-temperature heat source, such as high-pressure die casting (HPDC) foundries or steel-making shops. In addition to offering uncompromising fire resistance, other factors for choosing HFC include OEM endorsements.
A properly maintained HFC-operated system can behave reliably. Ongoing maintenance requires regular sampling and analysis to protect against costly component damage. The impact of neglected maintenance will often result in unplanned downtime, which needs to be meticulously scheduled to minimize associated inconvenience and revenue losses. Therefore, the long-term cost efficiencies and safety benefits of HFC are beyond question with an effective maintenance plan in place.
Four key maintenance parameters for HFC fluids
1. Viscosity
Water-glycol fluid viscosity is directly related to its water content. The glycol and polyalkylene glycol (PAG) thickener in an HFC fluid are not volatile and remain in the hydraulic reservoir regardless of fluid temperature. As such, the fluid’s viscosity is expected to increase over time as water evaporates.
The viscosity increase rate depends on ambient temperature, reservoir temperature, airflow across the reservoir breather, the amount of make-up fluid added, and other factors. A knowledgeable hydraulic fluid supplier can provide a graph that directly relates the viscosity to the water content. The graph eliminates the need to run actual water contents and allows for easy maintenance.
Decreasing viscosity can be related to excess water in the water-glycol fluid. This excess water can only come from a leaking heat exchanger or an over-addition of water during a water adjustment.
If a water alteration is necessary, perform water suppletion gradually and use soft, distilled, or deionized water. Divalent metal ions, such as calcium and magnesium found in tap and spring water, will separate the lubrication additive from the fluid, resulting in performance issues.
2. pH
The pH of the water-based HFC fluid must be above 8.0 to inhibit rust. A pH of less than 8.0 indicates that the system has been contaminated or diluted.
Alkanolamine chemistry must be used to raise the pH, as caustic materials like sodium hydroxide will not inhibit rust. However, the pH of the fluid in use will drop due to the loss of the vapor phase corrosion inhibitor. This is expected, as the vapor phase corrosion inhibitor is volatile and must leave the body of the fluid to inhibit rust in the vapor space above the fluid in the reservoir.
Quaker Houghton, for example, uses a dual amine additive system that ensures that the pH of the fluid in use will remain above 8.0.
3. Alkaline reserve
An alkaline reserve of 90 or above is needed to inhibit vapor phase rust in an HFC fluid. The alkaline reserve will drop with use because the vapor phase inhibitor is slowly removed from the fluid. The evaporation rate depends on reservoir temperature, ambient temperature, and airflow across the reservoir’s breather. Small additions of make-up fluid can significantly and positively impact the alkaline reserve of a water-glycol fluid. Depending on the amine used as the vapor phase corrosion inhibitor, the alkaline reserve of the fluid in service may never need to be adjusted.
4. Particle count
Particle counts must be managed to maximize component life. Pump and valve OEMs recommend fluid particle counts depending on pump type, operating pressure, and whether servo or proportional valves are used. Therefore, users can set particle count targets for a given piece of equipment by identifying the critical hardware in a hydraulic system.
Typically, water-glycol fluid will have particle counts around 19/17/14 as determined using the ISO 4406:1999 standard. This applies to fluid supplied in drums and intermediate bulk containers.
Obtaining accurate counts using ISO 4406 requires crystal-clear fluid. Hazy fluid will introduce errors in the particle counts. Other methods, such as particle resuspension, can provide better results and trending analysis but are not completely accurate. Reviewing OEM fluid cleanliness guidelines and speaking with the fluid supplier will help establish cleanliness limits for the fluid in service.
This article was contributed by Ronald Knecht, Global OEM Manager of Hydraulics and Lubricants at Quaker Houghton.
Quaker Houghton Fire Resistant Hydraulic Fluids
fireresistantfluids.com
Leave a Reply