Few people think of the motor’s exclusion seals as key components in a piece of equipment, but these unsung heroes can make all the difference, particularly in harsh environments. When a motor’s pressure seal is compromised, the machine starts leaking oil into the environment, which immediately impacts your bottom line. Lost productivity and maintenance costs are the first items that come to mind, but environmental concerns and cleanup can also be very costly. An equally important consideration is what a leaking motor says about your machinery brand. Oil leaks attract dust immediately and an oily, dusty machine is not the image most OEMs are looking to conjure.
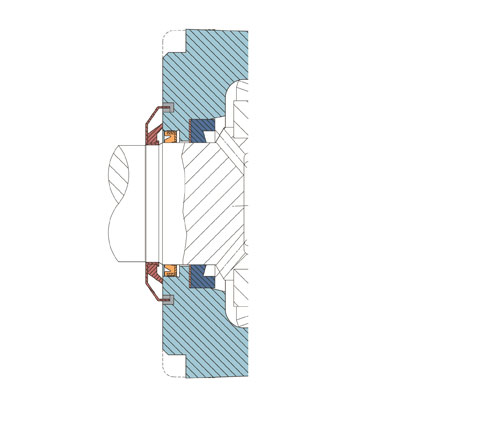
The number one failure mode on hydraulic system components is oil leakage––so as the operating environment gets harsher, the critical importance of a seal becomes readily apparent.
Let’s start with the basics
Hydraulic motors utilize two types of seals—one to keep oil in and another to keep dust and dirt out. Holding the oil in the motor is the function of a pressure seal, which can be designed to withstand low pressures, standard pressures, high pressures or even special pressure fluctuations, depending on the application. Pressure seals are sensitive to dirt and other contamination, so an exclusion seal—designed to keep contaminants out, is used to protect it from the outside environment.
These seals have a similar look to pressure seals but are installed in reverse to keep typical contaminates out—dust, dirt, grime, moisture, etc. However, outdoor environments are rarely “typical” and more challenging environments call for additional protection in the form of a slinger seal, also known as a seal guard, or a triple lip seal. These seals all provide the same function of protecting the pressure seal.
Types of exclusion seals
Standard exclusion seals include a rubber seal on the motor shaft that will keep dirt out for most applications.
Designed for harsher applications, such as brushes, sweepers or conveyers, a slinger seal is considered an additional layer of protection. Working in tandem with the standard rubber seal, a slinger seal is pressed onto the motor shaft, and rotates with the shaft to better protect from weeds, and stringing material, dirt, rocks or direct contact, like the water stream of a power washer.
For 15 years, the slinger seal has been considered the industry standard for the next level of motor protection in harsh applications. This seal does an excellent job, but has limitations when the motor is exposed to fine dust, and /or liquid solutions that can wash behind the rotating guard. A classic example is a salt melt solution that will easily flow around the guard and then dry out, crystalizing and corroding the shaft or damaging the exclusion lip. This is a common problem as more and more motors are exposed to salt/sand, chemical, or even crop harvesting applications, such as sugarcane, where juices of the harvested plants can be corrosive and solidify after breaching the slinger seal.
What is an OEM to do?
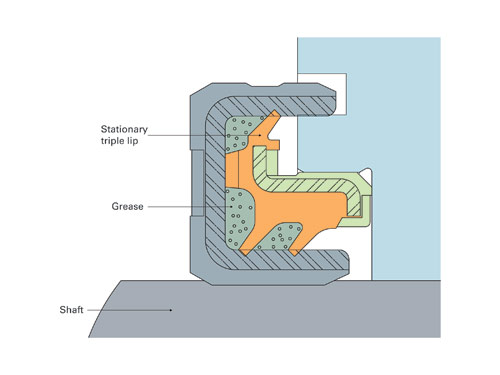
A new protection option is also available to help protect motors operating in the most strenuous environments, such as the sugar and salt examples outlined above, as well as cement augers, dredgers, sand vehicles, fertilizer spreaders, tillers and anything requiring a power wash down at the end of the day. The Extreme Duty Seal Guard is a two-piece design, with a pressed in stationary housing as well as the metal shield rotating with the shaft. It keeps the effective shield of the slinger/seal guard, but adds three additional lips that are packed with grease to keep dust and liquid fluids out. As the premium protection, the Extreme Duty Seal Guard, can outlast a slinger seal four times over, extending the life of on the motor and thus the machine in question.
Advanced sealing
Consider a salt spreader, and the concern about salt melt solutions discussed earlier. Salt is a caustic material that dissolves in water, settling into every crack and crevice of a machine. Most salt spreaders are regularly washed down to help avoid this, but during cleaning, water can get behind the seal—carrying salt particles with it—and degrade the shaft over time. Many owners and operators of salt spreading equipment expect a motor to last only two seasons of work, and build biennial motor replacement into the budget and maintenance schedule.
Machines like rototillers, cement augers and dredgers face similarly tough environments. Salt water and mud can be very hard on seals, especially submerged shafts that have to withstand the deflection and vibration of harsh digging. Servicing a dredger, for example, is a routine task for maintenance teams. However, installation of the extreme duty seal on these applications can extend maintenance intervals well beyond expectations. Further, many cement auger designs waste a lot of axial space and weight—up to 2 in.—doing the same thing the extreme duty seal guard can do in less than a ¼ in.!
While budgeting for maintenance costs is wise, the lingering question is whether or not so much maintenance should be required. What seemingly small changes can be made—without impacting the overall machine design—to improve this cycle of constant maintenance? Choosing the correct seal for your application can make a huge difference in the long run. When designing a machine, it is important to consider the environment the motor will face in day-to-day operation. In machines facing particularly harsh working conditions, simply choosing more powerful exclusion seals gives machine designers the power to significantly extend the life of the motor without major changes to the machine.
Contributed by Todd Degler, product manager, Geroler Motors, Gear Products, Eaton
I have a question a few questions I hope you can answer. First, does an excluder seal need to be lubricated. Since its job is to project the pressure seal I assume there should be no oil in that area. Also am I understanding correctly that they are completely separate seals. Or are they two seals in one. Can they be combined to be one seal. I have seen allot of seals that use these lips. is there any other way to prevent dust from getting through
The excluder seal is lubricated at factory and does not need regular or additional lubrication. The pressure and extruder seals are separate seals. Eaton does have many seal designs, some that are design for specific applications. The separate excluder seal, your referring to is a general purpose solution. For higher protection, a slinger or Extreme Duty Seal is recommended.
Thanks