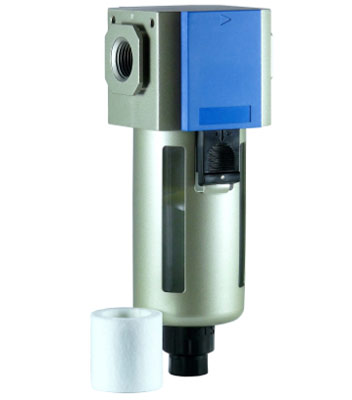
Large contaminants in a pneumatic system are readily captured by general-purpose filters or tend to settle out of a compressed-air stream. Air dryers can effectively remove water from compressed air. But aerosols—extremely small (≥ 0.1 micron) solid particles and liquid droplets of oil and water suspended in the air—remain in the flow stream and can cause problems downstream. This is where a coalescing filter come into play.
For example, these contaminants can hurt the performance of close-tolerance valves and instruments, damage seals, erode hose inner tubes and foul desiccant dryers. And they can adversely affect processes like paint spraying and contaminate end products such as food, beverages and pharmaceuticals.
Standard particulate filters do not remove most submicron contaminants. Coalescing filters, on the other hand, are designed to trap and subsequently remove submicron-size liquid oil and water and solid-particulate contamination from compressed air.
Coalescing filter elements have extremely fine fiber meshes that intercept and capture aerosol particles. They amalgamate smaller particles into larger ones. Tiny liquid droplets are brought together into larger droplets as air flows through the element’s fiber matrix, and they eventually become large enough to be drained away.
Coalescing filter elements remove contaminants using three different mechanisms:
Diffusion typically applies to particles 0.1 micron and smaller. These are subject to random Brownian motion and they collide with and are trapped by the filter. Solids adhere to the filter membranes and liquids join with other droplets to form larger masses.
Interception affects particles about 0.1 to 1 micron in size. Turbulent flow forces particles against the fibers, and they are captured in the filter matrix. Smaller pore size increases capture efficiency.
Direct impact applies to particles 1 micron and larger. Here, contaminants simply collide with and are trapped by the fibers.
In a typical coalescing filter, air enters the housing and flows through the media from the inside to the outside of the filter element. Coalesced oil and water droplets collect on the filter fibers and, as they grow in size, migrate downward due to gravity. The liquids collect in a bowl at the base of the housing and are subsequently drained away, while clean air exits the housing through the outlet port.
Coalescing filters also remove solid contaminants such as dirt, dust and rust from compressed-air systems. These particles are permanently trapped in the filter element, eventually restricting flow and blocking the filter media. So the volume, efficiency and degree of contamination of the incoming air help determine the useful life of the filter element.
In addition to common selection parameters like pressure limits and flow capacity, the units are rated by filter efficiency—a measure of the percentage of contaminants of a specified micron size that the element captures. Filter ratings vary by product and can range from around 90% to more than 99.99%. Users generally should specify products based on the application requirements, because more efficient filters typically cost more, have a higher pressure drop and shorter service lives.
How and where a coalescing filter is installed can also have a sizeable effect on overall performance and operating expense. Experts generally recommend installing a prefilter, such as a 3-micron unit, to remove as much as possible of the particles before it reaches the coalescer. This can significantly increase the life of the coalescing filter.
If the compressed air in a process has various cleanliness requirements in different circuits, install coalescing filters only in point-of-use locations that actually demand extremely clean air. This saves money. Also note that coalescing filters will cause a 2 to 6 psi drop downstream, so factor the pressure loss into the equipment sizing and selection. And, as with other filters, replace them whenever they become clogged. When pressure drop across the filter increases to 8 to 10 psi, that is an early warning sign that the filter is nearing its end of life and needs to be replaced.
Finally, note that coalescing filters do not remove oil vapor. Use activated-carbon or adsorption filters along with a coalescing unit when extremely clean air, such as breathing air, is necessary.
Leave a Reply